Sustainable
Technology
Our patented technology extracts ‘long’ and ‘short’ bamboo fibers in various lengths and thicknesses, transforming bamboo into a sustainable bio-fiber for lightweight, high-performance composites
Why bamboo?
Bamboo fibers are both renewable and sustainable, making them a highly attractive alternative to conventional fossil-based materials such as steel, aluminum, glass, and carbon fibers. Compared to other natural fibers, bamboo is readily and uniquely suited for industrial applications. During its growth phase, bamboo sequesters significant amounts of CO₂ storing it in its culms and extensive root network. As a result, bamboo fibers start with a naturally negative CO₂ footprint, offering unmatched environmental advantages.
Carbon negative
Optimal Property Retention
No chemicals
With a density of 1.4g/cm³, lower than conventional materials for high performance at lighter weights.
Sequesters a high amount of CO₂ during its growth phase (up to 50t CO₂/ha/y).
Boasts a higher specific stiffness than many other conventional materials.
Bamboo's impressive growth rate reaches 1 meter daily, far outpacing other fiber materials.
Guarantees a continuous, eco-friendly resource, vital for long-term sustainability efforts.
Less prone to moisture induced performance degradation due to the hydrophobic lignin in bamboo fibers.
Decarbonizing the Future with Bamboo
From growth to production, our CO2-negative bamboo products redefine sustainability and innovation. Contact us to learn more about our climate-positive solutions and their possibilities.
How it works
Frequently asked questions
Are these short fibers produced as a by-product of the long fiber production?
The raw material needed for the production of short fiber(s) (mats) comes from short bamboo chips. The bamboo chips are by-products obtained during the production of the input material needed for long fiber production and during long fiber production itself. Hence, no bamboo is wasted in our production process and we are able to fully utilize the bamboo culms.
Can information be provided on the CO₂ footprint associated with bamboo fibers?
The high growth rate and biomass yield of bamboo result in a large CO₂ uptake. The CO₂ that is taken up by the plant is stored in both the culms as well as the extensive root network. This attributes to a CO₂ uptake during its growth phase up to 50t CO2/ha/y. The fiber production process of Bambooder only consumes electricity and no polluting chemicals are used. The electricity used is sourced 100% from European wind energy, resulting in a very low CO₂ emission during the process. The process combined with the CO₂ uptake result in a negative carbon footprint of our fibers after the extraction process.
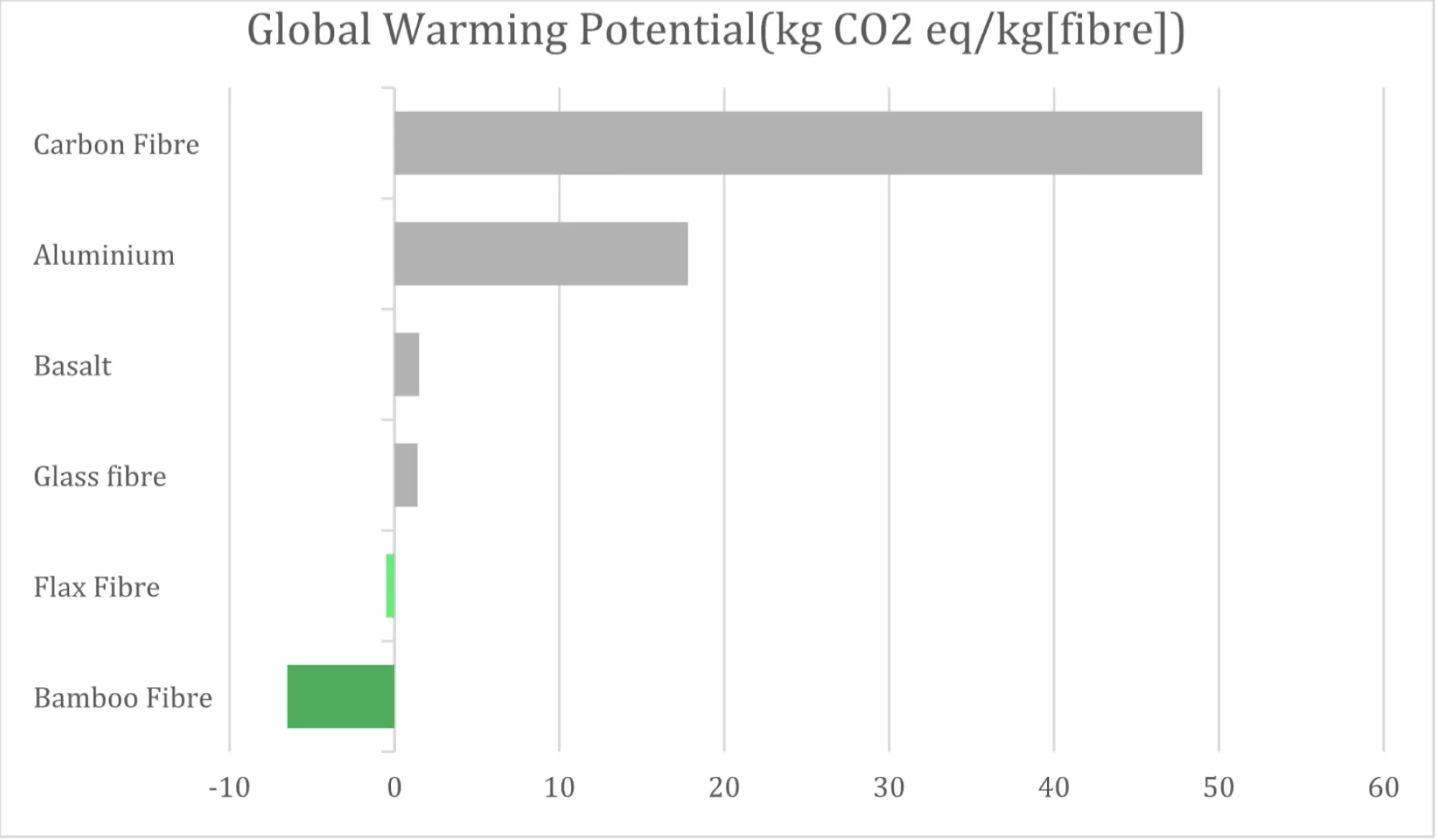
Is sizing applied for enhanced adhesion between fiber and matrix?
Bambooder does not yet apply sizings to the fibers to enhance the interfacial adhesion of fiber and matrix. We are currently developing a novel biobased sizing together with the Luxembourg Institute of Science and Technology that will improve the interfacial adhesion of the fiber and matrix and improve the thermal stability of the fibers.
What is the fiber volume fraction that can be achieved?
The fiber volume fraction of the long fiber yarns can be controlled according to the requirements of the customer. Standard, bambooder aims at is a fiber volume content of 95%. But bambooder can also produce prepreg yarns and generate a 50% fiber volume fraction.
Semi-finished products derived from the yarns (textiles/UD-tapes) can be processed into composites with commonly achieved fiber volume fractions just like any other glass or flax fiber textile or UD tape.
Short fiber mat thermoplastic prepregs are available with a fiber volume content between 30 and 70% depending on requirements for specific applications. For thermoset applications, the fiber volume content can be in the same range depending on the required performance for certain applications.
How abundant and sustainable is bamboo?
Bamboo is easily available due to its abundance in the world when compared to other commonly used natural fibers in the market. Over 30 milion hectares of bamboo are readily available. Bamboo has a growth phase lasting 6 to 7 months wherein the culms grow at a rate up to 1m/day. The growth phase is followed by a maturing phase wherein the culms gain strength. Generally, bamboo is harvest after 3 years with a yield of almost 40 t/ha/y. Additionally, bamboo sequesters a high amount of CO₂ during its growth phase (up to 50t CO₂/ha/y), which is stored in the culms and the extensive root network.

What is the shape of the bamboo fiber?
The fundamental fibers are tube-shaped cells with thickened walls, generally consisting of four layers around a central opening. Each layer is made up of semi-crystalline cellulose microfibers embedded in a hemicellulose/lignin matrix at a specific angle.
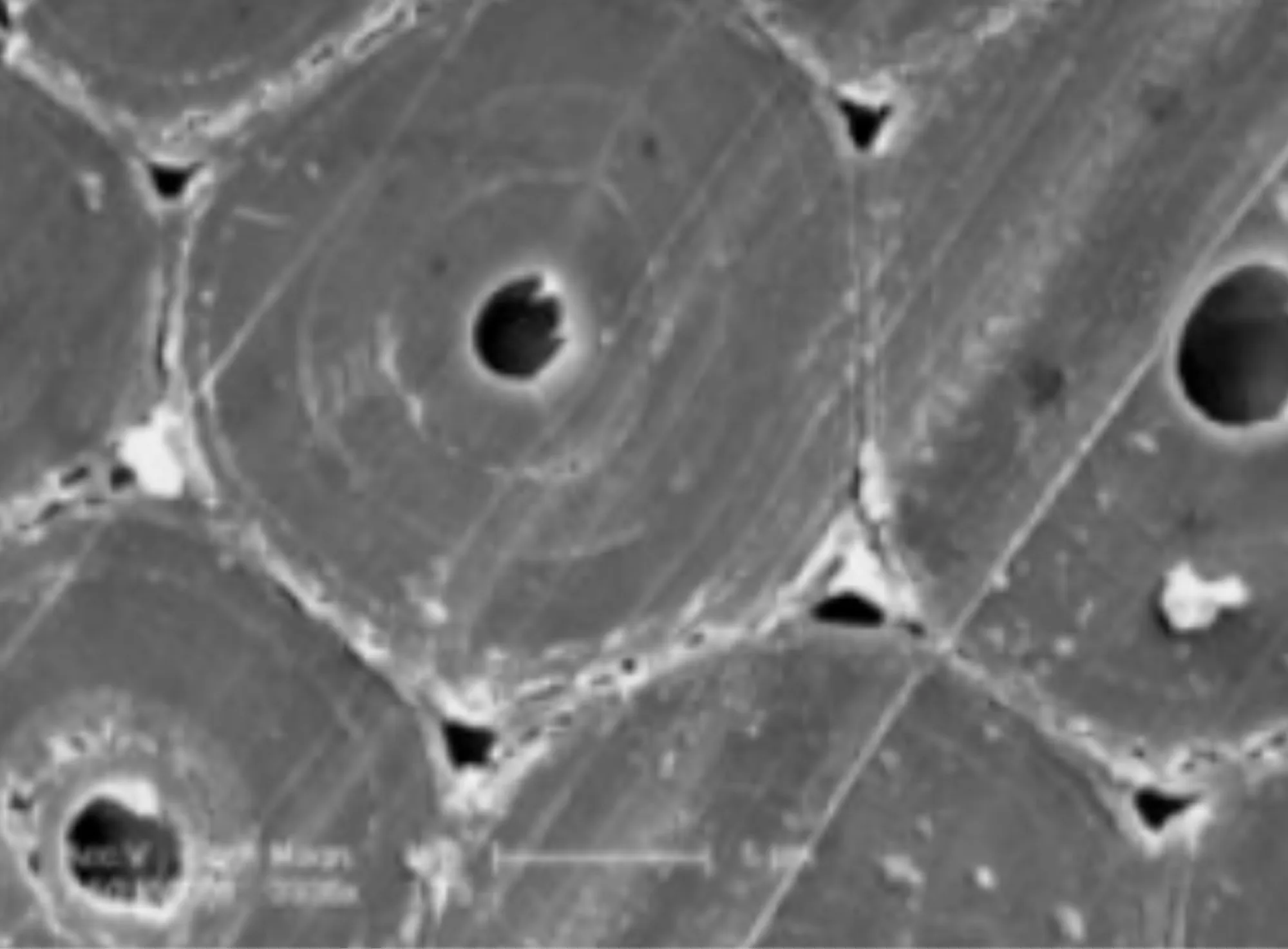